Application of Die Casting on Motorcycle Parts
Application of Die Casting on Motorcycle Parts
Die casting is a highly versatile process that can be used to produce small parts from many different materials. It can also be used to create complex geometries that are difficult to manufacture with other foundry processes.
The material used in the die-casting process determines its properties and impacts its design. It can also impact the machine and tooling that are used.
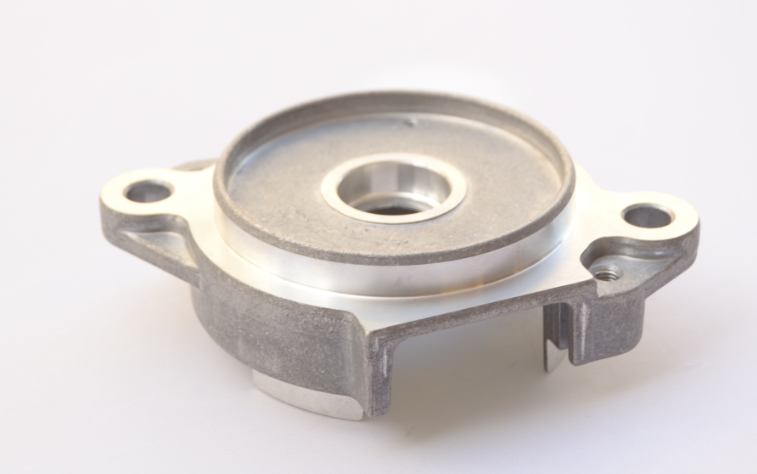
motor parts
Materials
Die casting is a process that is used to manufacture parts that are made from different materials. Various types of metals are used to make these parts, including steel and aluminum.
Steel is a material that is commonly used to manufacture motorcycle parts. It is known for its strength and durability. It is also easy to work with and can be shaped into many different shapes.
There are a lot of different types of steel, each with unique properties and characteristics. These include alloys that can withstand high temperatures and pressures,as well as other types that can be shaped into specific shapes.
Stainless steel is another common material used to manufacture motorcycle parts. It is often used for cylinder head covers, exhaust manifolds, rims, and frames. It is known for its resistance to corrosion and heat.
Magnesium is a lightweight metal that can be used to reduce the weight of a motorcycle. It is an excellent choice for lightweight parts, as it can help improve engine performance and fuel efficiency. It is also resistant to extreme heat and can be cast into intricate shapes. It is a great choice for motorcycle components that require a high degree of precision.
Zinc is another common alloy that is used to manufacture motorcycle parts. It is a low-density, non-toxic metal that can be cast into complex shapes.
The alloy used to make these parts can vary depending on the needs of the product. Some of the most popular alloys for die castings are magnesium and aluminum.
A magnesium alloy is a great choice for motorcycles that are intended for sport use. This alloy is 75% lighter than steel, 33% lighter than aluminum, and offers a high- strength-to-weight ratio that can help increase the durability of the motorcycle parts.
In addition to being lightweight, magnesium is also highly resistant to corrosion. This allows manufacturers to add more surface finishes in post treatment to their parts without sacrificing durability.
Stainless steel is another popular choice for die castings, as it is strong and durable. It is commonly used for cylinder heads, engine blocks, and transmission cases.
Design
There are many different dimensions to be considered when designing die cast motorcycle parts. Several factors can influence the final dimensions of the part, including material, design and application.
There is also a wide range of alloys that can be used for die casting, so it is important to know what will work best for the project at hand. For example, aluminum is often used in the cylinder blocks, cylinder heads and transmission cases of motorbikes because it’s lightweight, corrosion-resistant and conducts heat better than other metals.
While there are other materials that can be used in die casting, the most common options include zinc, copper, aluminum and lead / tin. Zinc, for example, is one of
the easiest metals to cast and has excellent ductility and impact strength.
Another popular choice is copper, which can be plated or polished and has high thermal and electrical conductivity as well as corrosion resistance. Copper can also be forged into custom shapes.
Magnesium is often used in ultra lightweight components because it offers a good combination of ductility and toughness. It’s also fully recyclable and has a high strength-to-weight ratio, making it ideal for applications where weight is a consideration.
In addition, it has a low density and is suitable for machining. This allows manufacturers to add extra features and improve the performance of their products by increasing their ductility, fluidity and mechanical properties.
The process of die casting involves forcing molten metal under high pressure into a mold, which has been prepared for the casting process. The metal will then cool and solidify as it enters the mold cavity, forming the final shape of the die cast part.
This is a relatively inexpensive manufacturing method, especially when compared to machining, which requires expensive tool steel dies. It’s also more efficient in terms of material usage: very little scrap is produced during the process, which reduces costs per unit.
It’s also a cost-effective way to produce highly detailed parts with close tolerances. It does require a lot of time, though, and it can be costly to create a new die for each production run.
Technology
Die casting is a process that forces molten metal into a mold cavity to form the desired parts. It is similar to the injection mold process but uses a different set of tooling.
The technology of die casting is used to create a wide variety of motorcycle parts. These include cylinder blocks, cylinder heads and transmission cases. These parts are made from aluminum alloy and are incredibly lightweight. They also improve the performance and fuel efficiency of a motorcycle engine.
Some of the most popular materials for die casting motorcycle parts are aluminium and magnesium. These are incredibly light, offer excellent strength-to-weight ratios and are fully recyclable.
In addition to these common alloys, you can also use specialized materials for specific applications. For example, the aluminum alloys used in cylinder blocks are lighter than steel and cast iron, which increases fuel efficiency and reduces engine damage.
Other popular material choices in the industry are titanium and stainless steel. These alloys provide exceptional corrosion resistance, excellent ductility and high strength-to-weight ratios. They are typically the most expensive of all the alloys, but they provide a number of other benefits.
Another common choice for small components is zinc. This alloy is a great choice for die casting because it offers high ductility, excellent dimensional accuracy and can be easily plated. Zinc is also a good choice for parts that need to be highly conductive, such as cooling radiators and oil lines.
Finally, copper is a popular choice for many automotive parts because it is easy to machine, has high impact strength and can be plated or painted. This is a particularly good choice for engine components, as it has the ability to conduct heat quickly and efficiently.
Die casting is an extremely efficient manufacturing process, and it can help you produce high quality motorcycle parts at a lower cost. In fact, you may be able to save up to 30% of the cost of your project by using this technique.
Production
Automotive die casting is a method that is used to make small spare parts in large batches. This technique is highly efficient and offers excellent finishes to the products.
The process can also be used to create complex parts with unusual shapes. This is a reason why it has become so popular among the industry. Many motorcycle manufacturers use this technology to produce their parts. These include cylinder heads, gas engine parts, mounting brackets and stators.
There are several types of die casting machines that are used to produce these parts. These can vary in terms of size and capacity, as well as the materials that they are made from.
Cold chamber die casting is the most common type of die casting machine. It is suited to working with various metals such as brass, steel, copper, nickel and iron.
Besides being inexpensive, it is also very fast and can be used to make many different types of parts. This makes it a great choice for high-volume production.
Sand casting is another type of die casting that involves pouring liquid metal into a mold. This technique is less expensive than die casting, but it can be difficult to create parts with thin walls.
The best choice of a die casting company depends on the part design and the materials that will be used. The company should have advanced equipment and strong technical knowledge to ensure that your product is produced to the highest quality possible.
Vacuum die casting is another popular method of producing small parts for motorcycles. This process is a good option for motorcycle makers that want to increase the strength of their parts. It is also a good choice for those that want to reduce the weight of their parts.
The most commonly used material for vacuum die cast parts is magnesium, which is a very light and tough metal. It is also resistant to corrosion, which can be a big advantage when it comes to making motorcycle parts.
Choose Selection Hardware
Selection Hardware is China professional die casting factory, we had produced high precision die casting parts for various industries, like automobile, motorcycle, machine, consumer electronics, medical equipment, fitness device, etc. We offer various raw material and surface finish options, and provide one-stop casting service, from prototype to shipping. If you have any custom needs for casting hardware parts, contact us now!